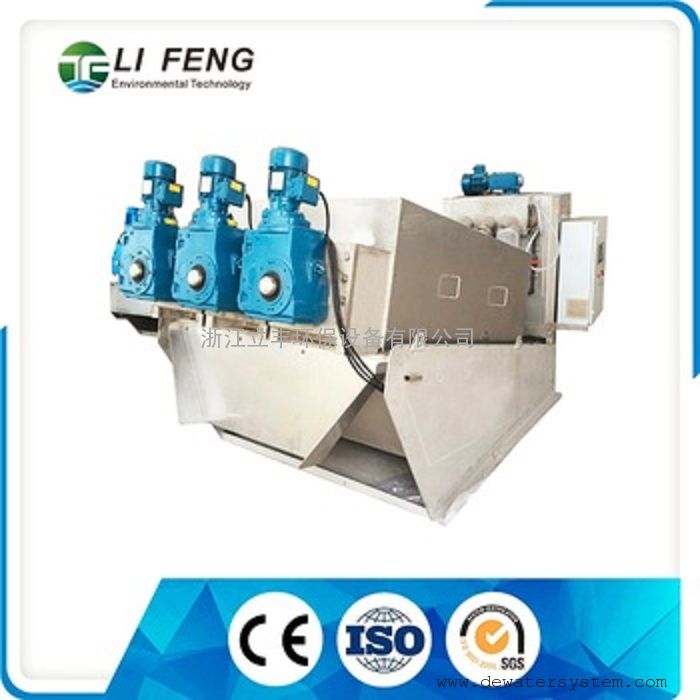
印染污泥
在印染废水处理中产生的大量污泥,经过“脱水—烘干—造粒—干 燥”之后,就“摇身”便成了污泥颗粒产品。这种热值较高、材料轻质的固体产品,既可以作为制砖的原料,又可以作为与煤混烧的燃料。
近日在江苏省吴江市盛泽镇污泥处理厂看到的景象。吴江市在全国率先建成了印染污泥资源化处置工程,使印染污泥的无害化处置,由昔日的“让人愁”变成了“惹人爱”。素有“日出万匹、衣被天下”美誉的吴江市盛泽镇,是我国历史上有名的四大绸都之一,如今又成为吴江市“纺织板块”中的“领头 羊”。历经多次产业结构大调整,在关停和取缔了数十家“小印染”之后,目前,全镇拥有规模印染企业27家,每天产生印染废水12.5万吨。为实现印染废水集中处理,吴江市先后在盛泽镇投入巨资,相继建成了7个镇级污水处理厂,形成了日处理印染废水17.5万吨的能力。随着市场化运营的步伐加快,7座污水处理厂先后由盛泽镇水处理发展公司“收购”并统一管理和运行。但是,盛泽镇印染废水实现集中处理后,由于印染废水处理产生的污泥量较大,每天产生的印染污泥量高达750吨,又成为吴江市环保工作上的一个“沉重包袱”。为及时处置这些污泥,过去,主要依靠填埋方法进行及时处置,既浪费了大量土地资源,又容易产生二次污染。大量印染污泥低水平的处置,已成为制约吴江市发展“纺织板块”的“瓶颈”,也成了吴江市决策层中的一块“心病”。为给印染污泥寻找资源化利用的新路,吴江市请来各路环保专家,共同为解决印染污泥献计献策。经过几次专题研究与探讨,确立了“污泥无害化、资源化处理”的攻关课题,用循环经济理念,来指导印染污泥处置和资源化利用。他们经过不断筛选和比较,*终确定引进浙江大学研制开发的污泥处置新技术,来化解印染污泥处置的尖锐矛盾。随后,由吴江市与浙江一家环保公司联合投资1000万元,建成了盛泽污泥处理厂,形成了日处理300多吨印染污泥处理能力。每天,盛泽污泥处理厂把从7座污水处理厂运来的含水率在93%的印染污泥,经过脱水机械对印染污泥进行压滤脱水之后,输进卧式烘干窑进行烘干处理,再将烘干之后的污泥,通过机械压制系统制成直径为1~4mm的污泥颗粒产品。盛泽污泥处理厂制成的印染污泥颗粒产品,具有较高的燃烧热值和质地较轻的特点,很快受到了江、浙两省交界地区燃煤企业和砖瓦厂的青睐。目前,盛泽污泥处理厂已发展长年利用印染污泥颗粒产品客户26家,实现了印染污泥颗粒产品“吃净用光”。吴江市在印染污泥处置领域开辟了一条新径,彻底改变了污泥倾倒与填埋的落后方式。印染污泥颗粒产品在制砖业的成功应用,已凸现出了喜人的三大效应:利用15%的污泥颗粒与粘土混合制砖,可以节约大量土地资源。污泥颗粒中含有较高的热量,在砖块烧制过程中,污泥颗粒又能够同时燃烧,并产生出2000大卡的热量,明显减少了烧制砖块的燃料。同时,利用污泥颗粒制砖,在烧制的过程中会在砖块内部产生均匀的圆孔,既可以增加砖块的强度,又可以减轻砖块的重量,给建筑物带来诸多的好处。印染污泥摇身变成颗粒产品,不仅彻底解决了污泥二次污染的弊端,而且产生了诱人的经济效益。按照传统的填埋方法,每天产生的750吨印染污泥,一年就要耗用100余亩的土地资源,一年仅耗用征用土地费用就达近1000万元。还有,过去依靠填埋的方法处理印染污泥,每吨处置费用为34.72元,全年处置费用达到800多万元。而生产颗粒产品之后,依靠“卖”印染污泥颗粒产品,一年就直接赚回270万吨。自从昔日“让人愁”的印染污泥,变成了“惹人爱”的污泥颗粒产品后,使吴江市政府更坚定了走“无害化、减量化、资源化”道路的信念。前不久,他们又积极筹措了600万元,完成了盛泽污泥处理厂的二期工程,使日“脱水—烘干—造粒—干燥”的能力扩大到了800吨。这样,盛泽镇每天产生的750万印染污泥就可以得到全部处置,转化成了颗粒状的产品。